Technical equipment
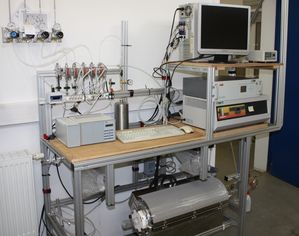
Catalyst test apparatus: The catalytic activity of catalysts in powder or monolithic form can be analysed in model exhaust gas under laboratory conditions. The characterisation of the catalyst activity is carried out in a laboratory flow-through apparatus, which contains two tubular reactors. Reactor 1 is used to characterise powder samples, while reactor 2 is suitable for monolithic samples. The samples are heated conventionally using a tube furnace. Catalysts are exposed to a model gas and the resulting temperature-turnover curves are recorded. Any volume flows, gas compositions or temperature ramps can be set. Samples can be analysed up to max. 800 °C with space velocities of at least 10,000 h-1 in the case of powder samples and up to 120,000 h-1 for monolithic samples. Already established gas components are O2, CO2, H2O, CH4, CO, NO, SO2, N2, CH2O, NO2.
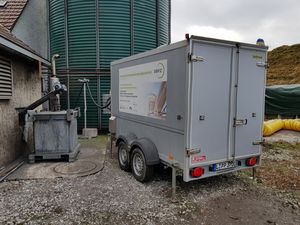
Mobile catalyst test apparatus: The mobile catalyst test facility is used for (long-term) testing of catalysts on a laboratory scale with real exhaust gas, e.g. from biogas CHPs. The system is designed for monolithic samples and works autonomously. Exhaust gas is extracted via a probe and passed through a reactor containing the catalyst. Before and after the catalytic converter, the change in gas composition can be recorded using a gas analyser. In addition, the temperature is recorded via several thermocouples. The system is built in a trailer and can be used at various field test locations.
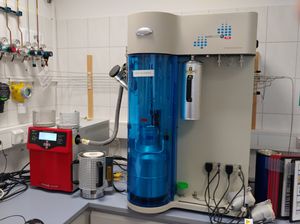
Solid state characterisation: Physisorption and chemisorption methods can be used to determine the textural and catalytic properties of both powdery and monolithic solids. Physisorption is used to analyse surfaces and pores in the micro- and mesoporous range. The adsorptive and measuring temperature can be varied. Nitrogen sorption isotherms are usually recorded at 77 K. Chemisorption is used in particular to characterise catalysts, in the course of this a distinction is made between the volumetric and the dynamic method. In addition to isothermal pulse titration, the dynamic method includes temperature-programmed reactions (reduction, oxidation, desorption), which are recorded using an integrated thermal conductivity detector and an optional downstream mass spectrometer. Mercury porosimetry is a method for determining the pore size distribution of accessible macro- and mesopores in solids. The technique is based on the pressure-dependent intrusion of mercury as a non-wetting liquid into a porous material. The He pycnometer is used to determine the volume of solids regardless of their geometric shape. This means that powdery and porous materials can also be analysed. The density of the sample is obtained by taking the mass into account. Possible analysis methods and measuring ranges of our devices can be found below:
- Physisorption and chemisorption analysis on powders and monoliths with N2 (77K); Ar (87K) und H2O (293K) - Analysis of spezific surface area and pore volume; H2-TPR; CO-TPR; TPO; NH3-TPD
- Hg porosimeter: Pore analysis on powders and solids in the range from 3,6 nm to 1000 µm
- He pycnometer: Density determination of powders, granules, porous materials and mixtures with a sample volumes in the range of 10-135 cm³
Combustion technical center: Our Combustion technical center includes test benches for characterising single-room heaters, biomass boilers, and biomass cookstoves. Appropriate emission measurement technology is available for characterization. This includes, among others, the following devices: particle number measurement with SMPS, ELPI, NPET; gravimetric particle measurement according to VDI 2066 with I.T.E.S. from Paul Gothe; characterisation of gaseous components with FTIR, Horiba gas analyzer, FID